寧國齒輪減速機生產廠家
發(fā)布時間:2025-01-09 01:02:52
寧國齒輪減速機生產廠家
1.加油量過多:在減速器運行期間,會劇烈攪動油底殼,并且潤滑油會散布在整個機器上。 2.減速機的結構設計不合理。 3.箱體內沒有回油槽,潤滑油積聚在軸封,端蓋,接頭表面等處,并在壓差作用下從間隙泄漏;檢查孔蓋太薄,擰緊螺栓后很容易變形,導致粘結表面不平整和接觸間隙漏油。 4.在減速機制造過程中,鑄件未經過退火或時效處理,內部零件也未拆除。不可避免地,應力和變形會導致間隙和泄漏;5.軸封結構設計不切實際。早期的減速機主要采用油槽和毛氈環(huán)式軸封結構,并且毛氈在組裝過程中因壓縮而變形,并且密封接合面之間的間隙。如果軸頸與密封件的接觸不理想,則由于毛氈補償非常低,密封將很快失效。機油槽有一個回油孔,但很容易堵塞并且很難獲得回油效果。 6.減速機內部與外部之間的壓力差:在減速器運行期間,由于運動對的摩擦發(fā)熱和環(huán)境溫度的影響,減速機的溫度升高。如果沒有通風孔或通風孔被堵塞,則機器內部的壓力會逐漸升高。機器內部的溫度越高,與外界的壓力差就越大,并且壓力差會導致通過間隙進行潤滑。油可能就會泄漏。

寧國齒輪減速機生產廠家
蝸桿傳動由蝸桿和蝸輪組成,一般蝸桿為主動件。蝸桿和螺紋一樣有右旋和左旋之分蝸桿傳動,分別稱為右旋蝸桿和左旋蝸桿,蝸桿上只有一條螺旋線的稱為單頭蝸桿,即蝸桿轉一周,渦輪轉過一齒,若蝸桿上有兩條螺旋線,就稱為雙頭蝸桿,即蝸桿轉一周,渦輪轉過兩齒。1、蝸輪蝸桿減速機的結構很緊湊,關于它的體積也是很輕巧的的,蝸輪蝸桿減速機具有小型但是效率高的特點,具有很好的散熱性,它的熱交換性也很好。2、蝸輪蝸桿減速機的安裝也是比較簡易的,蝸輪蝸桿減速機具有靈活的特性,易于維護。其優(yōu)點還包括傳動的時候比較穩(wěn)定,噪音比較小,而且很耐用,是我們選購的一款好的產品。3、蝸輪蝸桿減速機的輸出的扭矩比較大,并且實用范圍很大,蝸輪蝸桿減速機具有很高的安全可靠性,對我們的使用有很大的好處。

寧國齒輪減速機生產廠家
行星齒輪減速機運行平穩(wěn)、抗沖擊力與振動能力強。行星齒輪減速機采用了數(shù)個結構相同的行星輪,分布于太陽輪的周圍,可使行星輪與轉臂的力相互平衡,所以行星齒輪減速機的抗沖擊能力強、工作性能可靠。行星齒輪減速機傳動比大,傳動效率更高,可實現(xiàn)運動的合成與分解,行星齒輪減速機只要使用合適的傳動類型及配齒方案,即可獲得較大的傳動比,其傳動比可達上千。因為行星齒輪減速機的齒輪傳動對稱,具有均勻分布的行星輪,使作用于太陽輪與轉臂中的反作用力相互平衡,大大提高了傳動效率。行星齒輪減速機,體積更小、重量更輕、負載能力更大,行星齒輪減速機能合理的應用內嚙合齒及具有功率分流和各中心輪構成共軸線式的傳動,因此結構非常緊湊。

寧國齒輪減速機生產廠家
1、硬齒面減速機的齒輪軸選材方面對于傳遞動力為主的軸,應根據(jù)所傳遞的扭矩大小和與之相適應的軸頸大小,選擇高淬透性的,更優(yōu)越的調質鋼,但從金相分析可知,小齒軸的材質有疏松組織,夾雜物超級,結果使沖擊韌度下降,且在高變載荷作用下,裂紋迅速擴展,導致斷裂。 2、結構設計方面軸肩處由于堆焊修補后,幾乎無過渡圓角,造成嚴重的應力集中,在彎曲應力作用下產生疲勞裂紋,這是軸斷裂的主要原因。 3、熱處理方面在進行堆焊修復前,未按要求進行預熱處理,出現(xiàn)焊接區(qū)周圍組織的差異,此差異存在于狹窄區(qū)域內,會產生高的內應力,由于這種內應力的作用,在相變之后立即產生裂紋,導致斷裂,其次軸堆焊修復后,又未采取適當?shù)臒崽幚恚附託堄鄳^大,使軸抗交變應力下降,一旦遇上振動,就極易產生裂紋,以致發(fā)生斷裂。
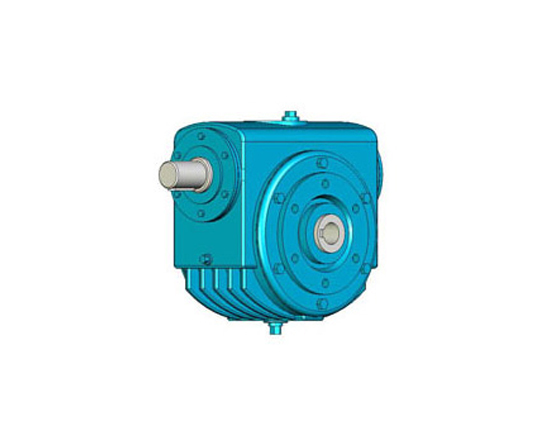
寧國齒輪減速機生產廠家
相對其他齒輪減速機廠產品,行星減速機具有高剛性、高精度、高傳動效率、高的扭矩/體積比、終身免維護等特點。因為這些特點,行星減速機多數(shù)是安裝在步進電機和伺服電機上,用來降低轉速,提升扭矩,匹配慣量。齒輪減速機廠產品額定輸入轉速最高可達到18000rpm以上,工作溫度一般在-25℃到100℃左右,通過改變潤滑脂可改變其工作溫度。精密齒輪減速機廠產品因搭配伺服電機所以背隙等級(弧分)相當重要,不同背隙等級價格差異相當大,行星減速機可做多齒箱連結最高減速比達100000。

寧國齒輪減速機生產廠家
齒輪減速機速比的常見計算方式:1、速比定義計算方法:減速比=輸入轉速÷輸出轉速。(比如輸入轉數(shù)為1450,輸出轉數(shù)為50,得出的速經就是29。其速比越大,輸出扭矩就越大,輸出轉速就越慢)。2、通用計算方法:減速比=使用扭矩÷9550÷電機功率×電機功率輸入轉數(shù)÷使用系數(shù)。(電機額定功率為P (kw),轉速為n1 (r/min),減速器總傳動比i,傳動效率u)3、齒輪計算方法:減速比=大齒輪齒數(shù)÷小齒輪齒數(shù)4、皮帶、鏈條及摩擦輪減速比計算方法:減速比=從動輪直徑÷主動輪直徑。5 減速機扭矩計算 9550×電機功率千瓦(0.55KW)÷電機轉速(1390)×減速機速比×減速機效率=扭矩NM。